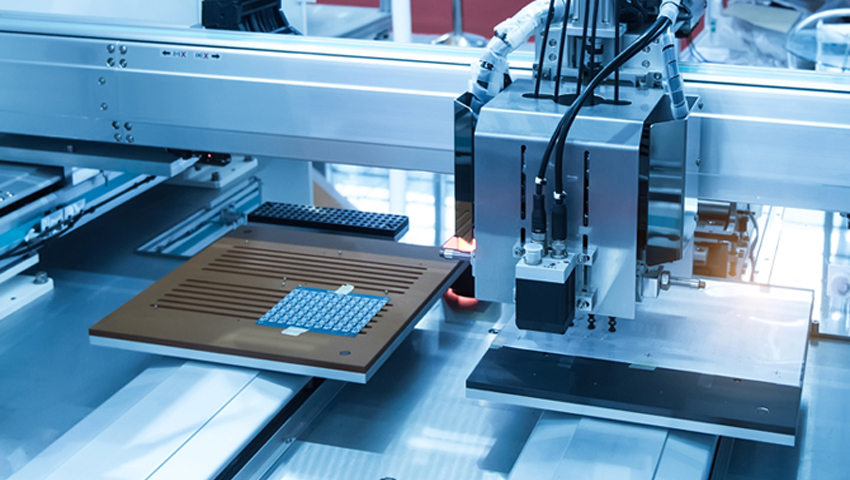
In the dynamic landscape of semiconductor inspection, Light Emitting Diode (LED) light sources have emerged as indispensable tools, revolutionizing the precision and efficiency of the detection process. Here’s a closer look at the pivotal role played by LED light sources in the semiconductor inspection industry:
1. Microscopic Inspection:
- LED light sources are deployed in high-powered microscopes for detailed semiconductor component inspection. Their ability to produce intense and focused illumination aids in identifying microscopic defects and irregularities with unparalleled clarity.
2. Defect Detection and Sorting:
- LEDs contribute to the accuracy of defect detection systems by providing consistent and uniform illumination. This is crucial in sorting and categorizing semiconductor components based on their quality and functionality.
3. Wafer Inspection:
- LED light sources are integral in the inspection of semiconductor wafers. Their precise wavelength control allows for targeted illumination, enabling the detection of imperfections, contaminants, or irregularities in the manufacturing process.
4. Photolithography Alignment:
- LED light sources play a vital role in photolithography processes by providing the necessary illumination for alignment and patterning. Their small form factor and directional light emission enhance the precision required for intricate semiconductor patterning.
5. Fluorescence Imaging:
- In semiconductor analysis that involves fluorescence imaging, LEDs are chosen for their ability to emit specific wavelengths. This is particularly valuable in identifying and characterizing semiconductor materials and structures.
6. Non-Destructive Testing:
- LED light sources enable non-destructive testing methods in semiconductor inspection. Their ability to produce controlled and non-invasive illumination is critical in assessing the integrity of semiconductor components without causing damage.
7. UV Inspection:
- UV LED light sources find application in the inspection of semiconductor materials sensitive to ultraviolet light. This includes detecting contaminants, ensuring uniform coatings, and examining the quality of materials under specific wavelengths.
8. Surface Inspection:
- LED light sources provide uniform and directed lighting for surface inspection of semiconductor components. This aids in identifying scratches, particles, or irregularities on the surface that could impact the functionality of the semiconductor.
9. High-Speed Inspection Systems:
- The instant on/off capabilities of LEDs contribute to the speed and efficiency of high-speed inspection systems. This is essential for maintaining production throughput in semiconductor manufacturing environments.
10. Energy Efficiency and Cost Savings: – LED light sources are known for their energy efficiency and long lifespan, resulting in cost savings for semiconductor inspection facilities. The reduced need for frequent bulb replacements and lower energy consumption contribute to sustainable and economical practices.
In conclusion, the incorporation of LED light sources in the semiconductor inspection industry marks a significant advancement in precision, efficiency, and reliability. As technology continues to evolve, the role of LEDs in semiconductor inspection is expected to further enhance the industry’s capabilities in ensuring the quality and functionality of semiconductor components.