We are committed to delivering quality products to our customers. Using advanced technologies and stringent manufacturing standards, we bring exceptional performance, reliability, and longevity to every LED module manufactured in our global strategic partner facility.
Our LED
modules, PCB e Chip-on-Board (PANNOCCHIA) LEDs are applications Our products are widely used in various applications such as medical, life science,industrial equipment, non-destructive testing, and analytical equipment.
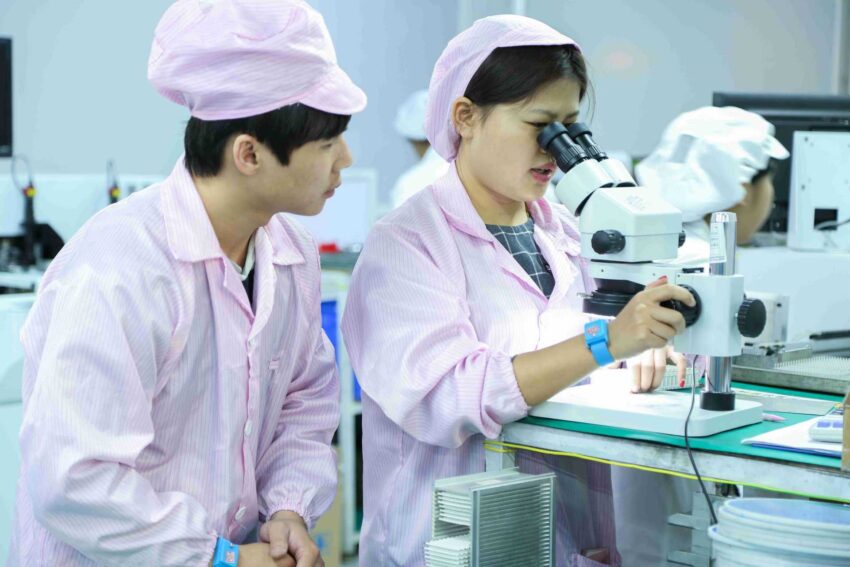
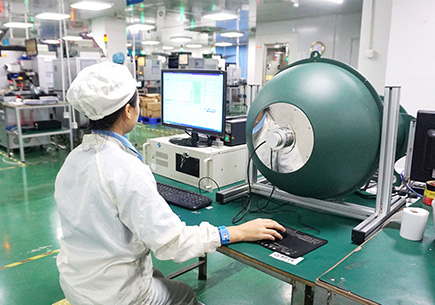
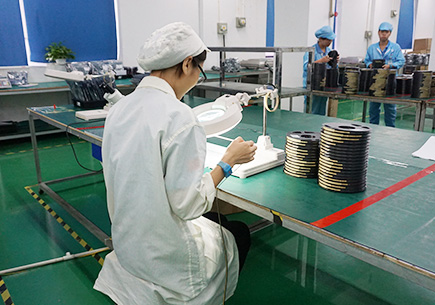

Our commitment to customer satisfaction is conveyed through QualityFIRST
Yingfeng delivers industry-leading quality services to customers through our QualityFIRST initiative.
Yingfeng recognizes the need to extend the quest for quality beyond manufacturing. QualityFIRST is embedded in our processes ensuring the same quality standards for all Yingfeng employees.
Yingfeng embraces the principles and concepts of QualityFIRST and incorporates them in all segments of our business from new product development to manufacturing, administration, sales and customer service.
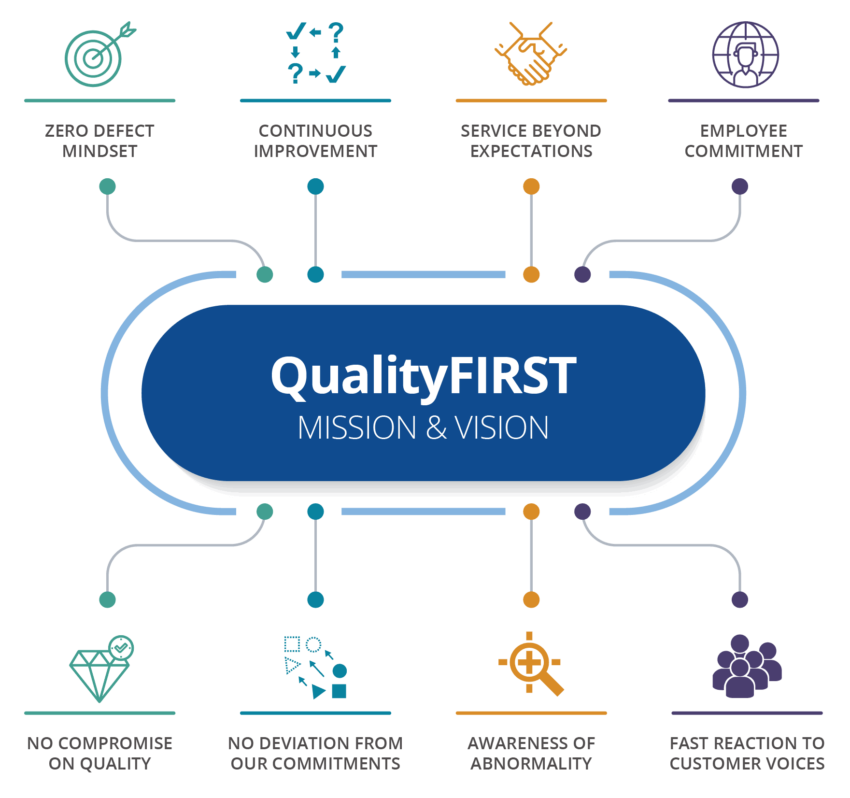
Quality management system
Each division has established and operates its own Quality Management System in compliance with the ISO 9001. In this system, items that are basic requirements are formalized in a “Quality Manual” and rules for design, development, purchasing, manufacture, inspection, shipping, and after-sales service are placed in document form to create a consistent quality assurance system.
Design and development
After drawing up plans to develop a new product based on market research or requests from customers, we start investigating the possibility of production in terms of product functions, reliability, and costs, eccetera. Based on results obtained from judging design details, verifying the design from prototypes, trial mass production, and reliability tests, we make sure the design is valid and then authorize the product. We also identify risks and opportunities in the process of design and development and promote product designs with a high degree of perfection.
Process management
The production process is supervised based on manufacturing specifications, QC process charts, and work standards to ensure that quality and reliability are at levels planned in the product design.To verify that the products meet the required specifications, Yingfeng performs process inspections and product inspections that check the product electrical/mechanical/optical characteristics and external appearance. The inspection items, methods, and test criteria are established in the product specifications. Destructive testing and lot evaluations are done by product sampling inspections.We make continuous improvements on production processes based on the results from statistical process control and KPI (Key Performance Indicator) monitoring.
Traceability
The manufacturing history and material lot used for a product that has been shipped are traceable. This enables us to determine a retroactive range at an early stage when a problem occurs.
Reliability testing
When a product is authorized or a change is made to a product, we make reliability tests to verify that a product meets the specified reliability requirements. Reliability tests are performed by selecting typical products from among a group of structurally similar products. If needed, this testing is performed individually. Reliability test methods conform to JIS, JEITA, IEC, or MIL standards, and also some products are tested according to customers’ requirement.
Measurement management
The quality control department periodically calibrates the test and measuring equipment. Calibration equipment is traceable to the national standards through the manufacturers and public organizations. Besides calibration, start-up inspections and periodic inspections are made to prevent and detect a drop in accuracy or a malfunction in the measuring equipment.
※Our reliability test equipment includes life test equipment, strength test equipment, transportation test equipment, radiation exposure test equipment, and others.
Production equipment management
When production equipment is implemented and authorized, it is given maintenance and verified for modifications or expansions. Specific methods for making start-up and periodic equipment inspections are established to perform preventive maintenance. Thus quality problems are prevented and stable production is maintained.
Procurement management
Procurement management of parts and materials has a large effect on product quality, so we use a system that judges and then registers both the suppliers and the parts and materials for purchasing.
We carry out an inspection of the suppliers to check compliance with quality environment system, green procurement policy, regulations regarding the chemical substances contained in products, and other factors. We then register those suppliers who meet our standards and also make new and periodic supplier audits mainly by the purchasing, quality control, and design departments. We strive to improve the quality of parts and materials for purchasing by giving proper guidance to the suppliers based on the audit results.Purchased items undergo strict individual testing and are then registered before they can be used in our products.An incoming inspection of those purchased items is then made based on the required specifications to verify their quality. After acceptance, these purchased items are stored in properly controlled locations that meet storage conditions specified in the design standards, and a high level of purchased item quality is maintained.
Dealing with process errors
When a problem occurs in the production process, which might cause defects that exceed preset process standards or might adversely affect the product quality, then the problematic lot is immediately identified and separated from other semi-finished parts. At the same time, the cause of the problem is investigated, and the corrective action that should be taken is decided. Along with confirming the corrective action was effective, we take measures to prevent the problem from reoccurring.
Change control
Changes such as in designs, purchased items, and production methods and equipment are made in order to improve product quality, function, reliability, and productivity. Change planning is first of all drawn up, the job schedule from change setup to completion is clarified, and the planning then finalized at a change conference attended by all related departments including quality control. Finally, the change is decided after evaluating effects on quality, reliability, and productivity, etc.Changes requiring the customer’s approval in advance are implemented after obtaining the customer’s consent. Initial production control is performed as needed and all effects caused by the change are checked.
Packing
We use special packing techniques and materials which are also environmentally friendly in order to safeguard product quality and prevent shipping damage.
Management of chemical substances in products
Environmental regulations, such as EU RoHS, REACH and China RoHS, have become stricter than ever in worldwide, thereby requiring companies to properly manage the chemicals contained in their products throughout their supply chains.We have organized a system inside the company in compliance with “Guidelines for the management of chemical substances in products” by JAMP/JGPSSI. We make sure to register and use materials complying with the guidelines by implementing green procurement and its survey to our suppliers based on our “Green Procurement Guidelines” E “Green Procurement Management Standard for Chemical Substances”. The survey results are stored in centralized information system for chemical substances in products, and used for actions to environmental regulations.